Олег Савченко о наступлении новой эры в судостроении
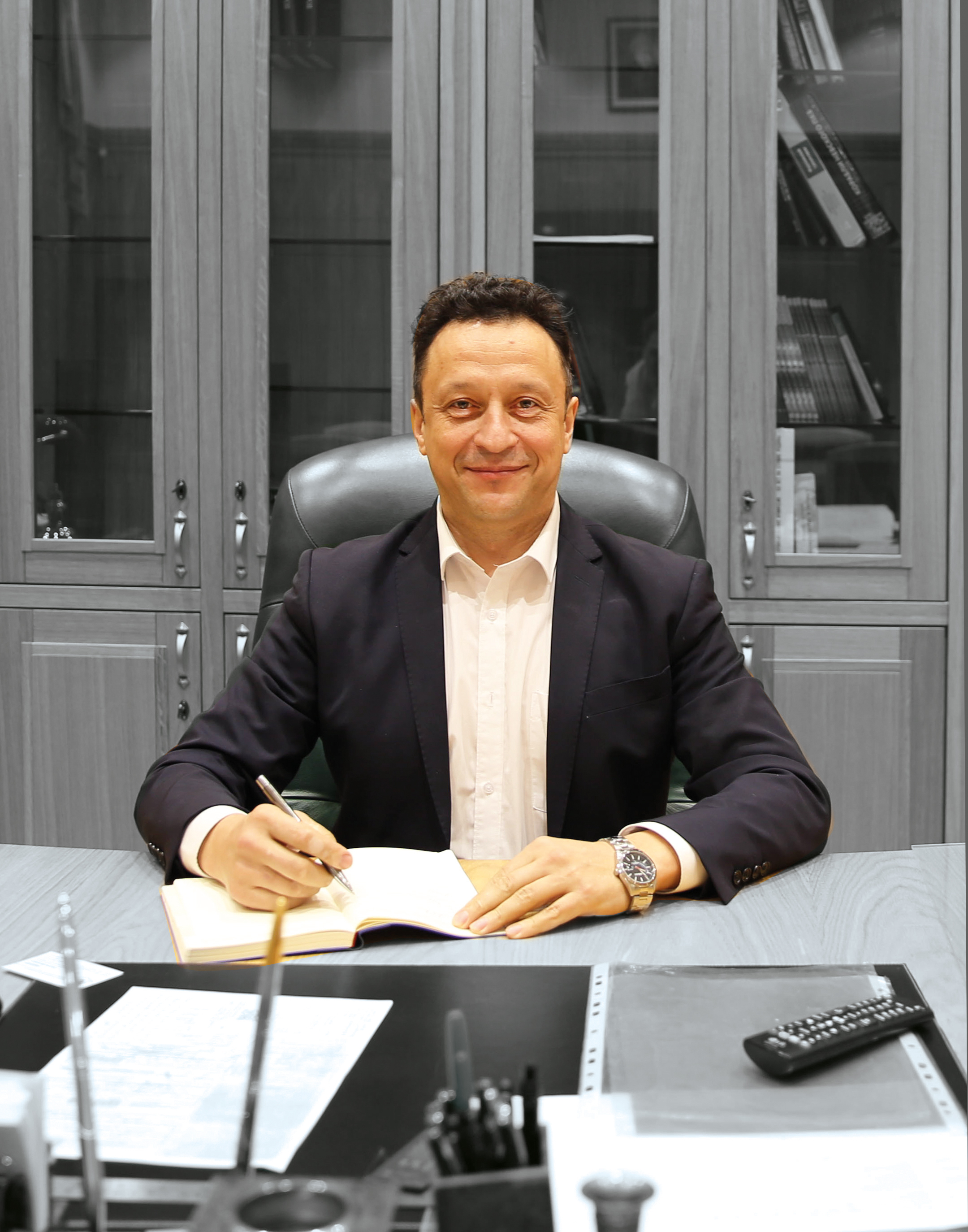
Перед научным и инженерным сообществом России поставлена задача обеспечить судовладельцев отечественными технологическими решениями. О том, как продвигается работа над проектами зерновозов и газовозов, почему сегодня мы не можем строить азиподы и когда решим проблему низкооборотных двигателей в интервью ИАА «ПортНьюс» рассказал генеральный директор Крыловского ГНЦ Олег Савченко.
— Олег Владиславович, планирует ли Крыловский ГНЦ показать на выставке «НЕВА 2023» новые разработки?
— Основной лейтмотив, который мы будем демонстрировать на «НЕВЕ» через общий дизайн нашего стенда и выставляемые на нем экспонаты, — это наступление новой эры в судостроении, эры, когда основным помощником отечественному судостроителю будет отечественная промышленность, отечественные технологии и отечественная наука.
Конечно, мы будем демонстрировать результаты нашей работы, которых мы достигли за последние 3-5 лет за счет интеграции трёх составляющих Крыловского центра. Во-первых, наших научных подразделений, которые занимаются прикладными исследованиями, опытно-экспериментальной работой, исследованиями в области новых технологий, связанных с созданием основного комплектующего оборудования, а также в целом судов и кораблей нового поколения.
Во-вторых, представим на выставке наше производство. У нас в «Крыловке» находится четыре производства под одной крышей: электро-техническое производство, на котором мы изготавливаем элементы уникальных систем; производство резинотехнических изделий, которое отвечает за апробацию технологий в области построения корабельно-судовых покрытий; производство систем, связанных со снижением электромагнитных полей, а также борьбы с судовой коррозией, и механическое производство.
Третья составляющая нашей экспозиции на выставке «НЕВА 2023» связана с разработкой концептуальных проектов и техническим проектированием судов и кораблей. Напомню, что в состав «Крыловки» входит старейшее в стране проектное бюро «Балтсудопроект», сформированное еще в 1925-м году.
— Будут ли представлены проекты зерновозов, которые вы разрабатываете по заказу Минсельхоза
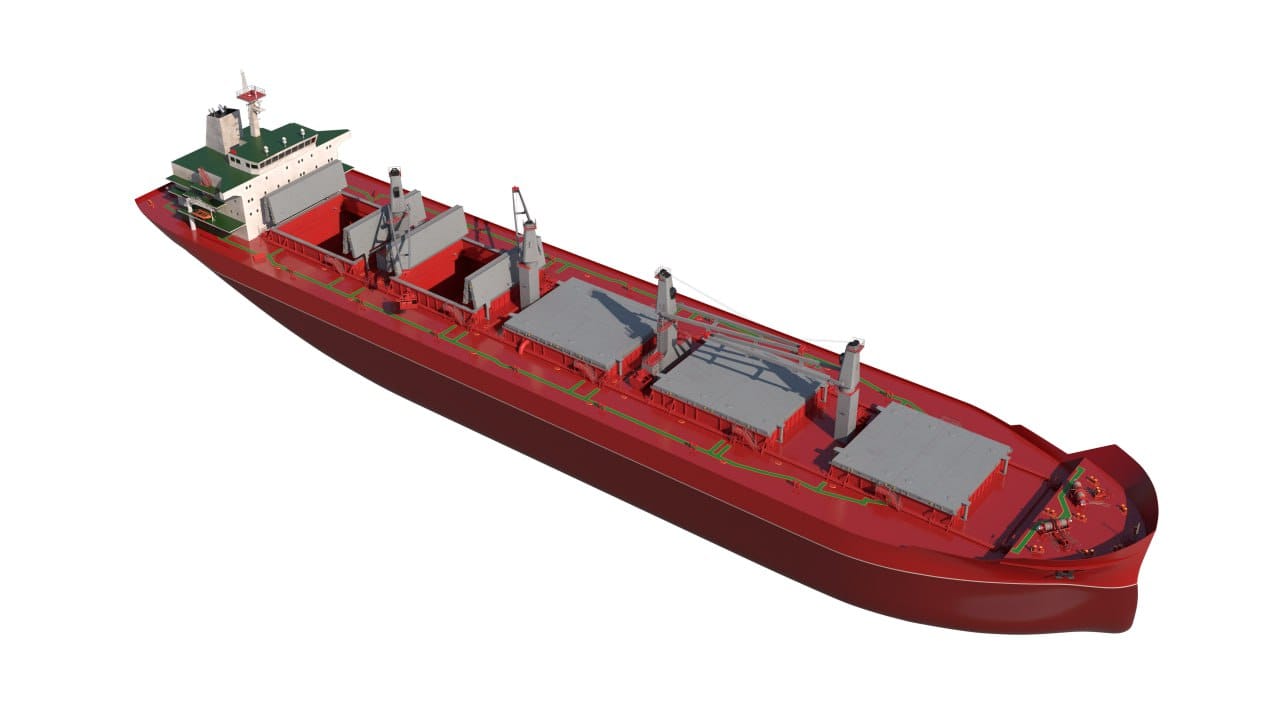
— Да, мы будем показывать промежуточные результаты технического проектирования балкеров-зерновозов, которое мы выполняем по контракту с Росагролизингом, подконтрольным Минсельхозу. Это первые российские проекты балкеров дедвейтом 40 тыс. тонн и 60 тыс. тонн. Они необходимы сейчас для обеспечения вывоза отечественных зерновых за рубеж.
Этот проект находится под личным контролем министра сельского хозяйства Дмитрия Николаевича Патрушева. Он неоднократно сам приезжал к нам в Крыловский центр с потенциальными судовладельцами, которые профессионально рассматривают текущие результаты работ и дают свою оценку. Оценивают, конечно, не всегда ожидаемо, но всегда конструктивно.
Перед нами поставлена задача в ноябре этого года завершить техническое проектирование и представить на защиту технологии строительства новых российских балкеров. То есть нам предстоит определить, на каких верфях эти суда будут строиться. Для этого выбора у нас есть свои подразделения, которые отвечают за технологические аудиты судостроительных предприятий, разработку программы размещения госзаказа по судостроительным верфям. Также мы работаем в тесном взаимодействии с АО «Центр технологии судостроения и судоремонта».
— Предварительно вы сможете назвать какие-то верфи, которые, на ваш взгляд, смогут построить эти балкеры? Ведь суда большого дедвейта в России сложно строить...
— Для начала хочу подчеркнуть, что планировать надо строительство серии новых балкеров. Сейчас мы не можем говорить за министерство сельского хозяйство и потенциальных судовладельцев о размере такой серии, но, по нашим оценкам, это должно быть несколько десятков судов.
Тут очень важно понимать, что фактическая загрузка тех немногих российских верфей, которые способны строить крупнотоннажные суда, очень высока. Например, технологическая основа для такого проекта есть у «Адмиралтейских верфей», и они смогут построить головное судно. Но верфь не сможет построить серию в силу большого числа других заказов. Дальневосточный ССК «Звезда» имеет шикарные паспортные данные, но текущая загрузка не позволяет нам планировать строительство балкеров на этой верфи.
Поэтому мы рассматриваем создание проекта распределённой верфи здесь, в Санкт-Петербурге. Финишная сборка может осуществляться как на Адмиралтейских верфях, так и на Кронштадтском морском заводе.
Важно понимать, что фактическая загрузка тех немногих российских верфей, которые способны строить крупнотоннажные суда, очень высока. |
— Какие основные сложности могут возникнуть с комплектующими в новых проектах?
— Мы занимаемся проблематикой создания балкера в условиях отсутствия приемлемой энергоустановки. Нам нужны низкооборотные реверсивные двигатели, которых в России пока не производят.
Хотя наработки Трансмашхолдинга в этом направлении очень интересны. Кирилл Валерьевич Липа (глава Трансмашхолдинга — прим. редакции) и его специалисты очень ответственно подходят к созданию именно российской технологии строительства дизелей. Действительно, результат их работы впечатляет. Они смотрят дальше, говорят о двухтопливных дизелях на сжиженном природном газе (СПГ).
При этом новый дизель раньше, чем через 5-7 лет не спроектируешь. Затем нужно изготовить опытный образец, провести его испытания, решив предварительно огромный круг проблем, связанных с испытательным оборудованием.
— То есть может пройти и 10 лет? Но если продолжать дорогостоящие и сложные разработки двухтопливных двигателей, они не окажутся через 10 лет ненужными? На ваш взгляд, потребность в газовых двигателях для судов сохранится?
— Несомненно, сохранится. При перевозке газа был и остается эффект отпаривания газа. И этот газ либо надо повторно сжижать и вводить в систему удерживания груза, либо его надо выкидывать, тогда маржинальные показатели падают, либо его надо использовать как бункерное топливо. Пока будут ходить газовозы с СПГ, будут нужны двухтопливные машины или даже однотопливные газовые машины. И Трансмашхолдинг ответственно работает над этим вопросом. Кроме него за более короткий срок никто не сможет начать производить эти двигатели в России.
Понятно, что такая высокотехнологичная продукция требует помощи от государства.
– Крыловский ГНЦ ведет разработку судна-газовоза. Как продвигается работа?
— Концепт отечественного газовоза мы разработали в тесном взаимодействии с подразделением Атомэнергомаша. Он в себя включает котло-турбинную установку, где предусмотрен двухтопливный котёл, который может работать на газе или на дизеле. Его энергоемкость ниже, чем у двухтопливного дизеля, то есть топлива потребуется больше процентов на 30-40.
Конечно, собственнику, судовладельцу экономическая модель применения этой энергоустановки может показаться не совсем приемлемой. Но на сегодняшний день для нас это единственное решение, если мы ставим задачу наращивания производства технологической мощности нашего государства. И мы должны честно сказать: «Коллеги, вы будете возить газ либо на этих пароходах, либо вообще возить его не будете». Но это уже не наше с вами решение, такие решения должно принимать политическое руководство страны.
— С уходом с российского рынка французской компании GTT как будет решаться проблема емкостей для СПГ?
— Еще в 2014 году у нас в «Крыловке» завершились ОКР по созданию принципиальной технологии системы удерживания груза (газа). Ведущим отделением по этой ОКР было отделение прочности. Они разработали технологии, обосновали, на каком отечественном сырье можно построить системы, подобные GTT. Сейчас, если встанет такая производственная задача, мы сможем ее решить примерно за полтора года. Технология у нас есть, материал отечественный есть, есть проблемы с клеями, но мы их решим. Нам надо создать опытный отсек, затем на базе опытного отсека создать стенд по проверке параметров, которые связаны с этой системой. Мы понимаем, как провести испытания и создать именно технологию, отечественную систему и сертификации материалов, и сертификации работ.
— После аудита завода «Звезда» Минпромторг и Росатом приняли предложение Роснефти о передвижке сроков строительства головного ледокола «Лидер» вправо на 2 года и увеличении его стоимости. На ваш взгляд, с чем это связано?
— Я скажу, что проект очень сложный, его проектирование и строительство непростое, ведь мы хотим построить самый большой в мире ледокол. Росатом обосновал необходимость строительства этого ледокола потребностью в проводках газовозов в восточной части Севморпути в условиях сплоченных тяжелых льдов, как, например, в Чукотском море. Есть альтернативные варианты, конечно, но хотелось бы получить этот ледокол к 2027 году.
Вообще, строительство ледокола — это сложный технологический процесс. Помимо большой потребности в квалифицированных рабочих, сварщиках, важно оценить, в каком состоянии основной комплекс производства. Потому что здесь будет новая реакторная установка, новая система электродвижения и тд. Завод может найти людские резервы, могут появиться китайские, индийские рабочие. Но если не из чего делать ледокол, то тут уже никакие внутренние резервы не помогут. Завод может просить сдвинуть сроки исполнения контракта не только по причине отставания корпусных работ, поэтому надо разбиратьс, в каком состоянии основные системы.
— Не так давно вы отмечали, что есть проблема исключения из практики проектирования комплексных проектных исследований, так называемой стадии концепт-проекта, как в военном, так гражданском судостроении. Изменилась ли ситуация?
— К сожалению, нет. Раньше была очень хорошая советская технология, связанная с принятием решений о проектировании и строительстве. Она предполагала наличие совокупных систем исследований, в том числе, исследований в рамках концепт-проектирования по номенклатуре, необходимой для народного хозяйства или ВМФ, судов и кораблей. То есть прежде чем начинать проектировать, надо понимать, «о чем» мы будем проектировать. Такую технологию в том или ином виде мы видим в ведущих в области судостроения зарубежных странах.
Например, «Акер Арктик» в Хельсинки. Они делают проект в объеме тендерного проекта. Это не технический проект, но он позволяет понимать, какой технический облик будет у судна, какие связаны с этим обликом системные характеристики, характеристики проходимости, ходкости, какие системы должны насыщать этот пароход. И в целом проект получает интегрированный параметр по строительству, в том числе экономический параметр по строительству. На мой взгляд, это признак нового уровня в судостроении, которого и мы должны добиваться.
Дальше идет работа на верфях, рабочим проектированием занимаются верфи. Основная экономия на оптимизации технологических решений происходит за счет проектного бюро верфей.
У нас же зачастую заказчик просит построить судно, которое удовлетворяет определённым требованиям. Но спросите заказчика, а почему судно должно удовлетворять этим требованиям? Понимает ли заказчик соответствие между требованиями и стоимостью, возможностями промышленности по реализации этих требований?
Это проблема, которая накрыла ОСК в части строительства кораблей, подводных лодок, когда требования выдвигались либо недостижимые, либо были необходимы огромные ресурсы промышленности, чтобы наладить производство чего-либо, обеспечивающее выполнение этого требования.
Поэтому, если мы хотим что-то поменять в судостроении, надо определить проектные организации и обеспечить им поддержку со стороны отраслевой науки. Первые небольшие шаги мы сейчас делаем. Вице-премьер правительства Денис Мантуров потребовал от ОСК перед началом строительства подвергать технический проект технико-экономической оценке. Шаг сделали и коллеги из ВПК, которые приняли документ под названием «Руководство по строительству кораблей» для ВМФ. В нем тоже есть обязательная экспертиза технического проекта. Эта система позволяет снизить только риск ошибок на этапе проектирования, однако могут происходить ошибки другого плана.
Поэтому при создании газовоза мы пошли таким путем: мы создали сначала концепт проекта, можно это назвать «эскизный проект», для того чтобы оценить его на уровне государственного заказчика и потенциальных судовладельцев. Для нас важно прояснить ситуацию: сегодня, если вы будете в России строить судно, — чуда не будет. То есть в ближайшие 6-7 лет не будет у газовоза двухтопливного двигателя, будет либо газотурбинный двигатель, либо котлотурбинный двигатель с такими-то расходами. Не будет и электрических рулевых колонок под названием «азипод», а будет прямая линия вала, и когда газовоз подойдет к порту, судовладельцу придется заказывать буксиры для обеспечения маневренности в порту. Другие технологические решения объективно появятся в России только через 6, 10, 12 лет.
Для нас важно прояснить ситуацию: сегодня, если вы будете в России строить судно — чуда не будет. То есть, в ближайшие 6-7 лет не будет у газовоза двухтопливного двигателя, будет либо газотурбинный двигатель, либо котлотурбинный двигатель с такими-то расходами. Не будет и электрических рулевых колонок под названием «азипод», а будет прямая линия вала |
— Можно ли из военного кораблестроения брать больше технологий для гражданского судостроения?
— Я вас уверяю, несмотря на то, что корабли и суда ходят по воде, там закладываются совершенно различные технологии, критерии, требования. И мы наблюдаем скорее обратный процесс — трансфер гражданских технологий в кораблестроение. Потому что свободного капитала в судостроении было больше, и мы там, в хорошем смысле, творили больше.
— Например, гребные винты мы успешно проектируем и производим для военного флота, почему же остается дефицит винтов для гражданских проектов?
— Для кораблей, в отличие от гражданских судов, требования проектирования жестче. Винты должны быть не только тяговитыми и прочными, но ещё и малошумными. Сегодня у нас достаточно компетенций для проектирования винта любого назначения, любого класса корабля и судна в России. И мы это делаем, к нам приходят заказчики за проектированием лопастной системы винта.
— Вы сказали, что мы не можем делать азиподы. Почему?
— «Крыловка» ведет разработку инновационных технологий, у нас была ОКР, по азиподу в кооперации с Ленинградским электромашиностроительным заводом. Азипод был сделан для проверки технологий, связанных с построением гондолы азипода, конструкции электрических машин, особенностей систем охлаждения, поворота, особенностей построения системы электродвижения. Эта работа упрощает для нас создание азипода, но его надо делать для конкретного судна: конкретный азипод с конкретным номиналом. Для этого надо разработать ГОСТ для разработки и постановки азипода на производство. Это требование «перепрыгнуть» нельзя. И эта работа требует, по моим оценкам, лет 5.
— Почему так долго?
— Потому что надо проектировать конкретный азипод, чтобы судно не переворачивалось, чтобы он сохранял маневренные качества, вписать в корпус конкретного судна, развесовку выполнить и т.д. На это уйдет год. Дальше нам необходимо под этот проект сделать основные конструктивные решения, спроектировать электрическую машину, поворотную систему, систему охлаждения, систему электродвижения. Технический проект — это еще год. Дальше — рабочее проектирование и изготовление. Допустим, за год сделаем. Ну, хорошо, вот вам 3 года, и появится свой азипод, но его еще надо будет испытать.
— Можно ли выстроить систему так, чтобы учитывать проектирование отдельных систем при проектировании судна?
— Традиционно у нас заказывают технический проект на судно, а все остальное делается в рамках контропоставочного контракта. А раньше при строительстве, например, высокотехнологичного корабля, авианосца, открывалась целая госпрограмма, в которую входила разработка обеспечивающих систем: электроустановки, катапульты и т.д. Вот пока технического проекта по составным частям не выполнено, технического проекта на весь корабль не будет. Пока рабочей документации на составные части нет, «рабочки» на корабль — нет.
Я бы хотел, чтобы мы вернулись к старой системе. Иначе мы будем в очередной раз верить в чудо, но чуда не будет, потому что нет готовых систем, нет лицензионных двухтопливных двигателей, нет азиподов. Нам самим предстоит это разрабатывать и делать.